Inventory Costing Methods: Guide to Choose the Best Approach
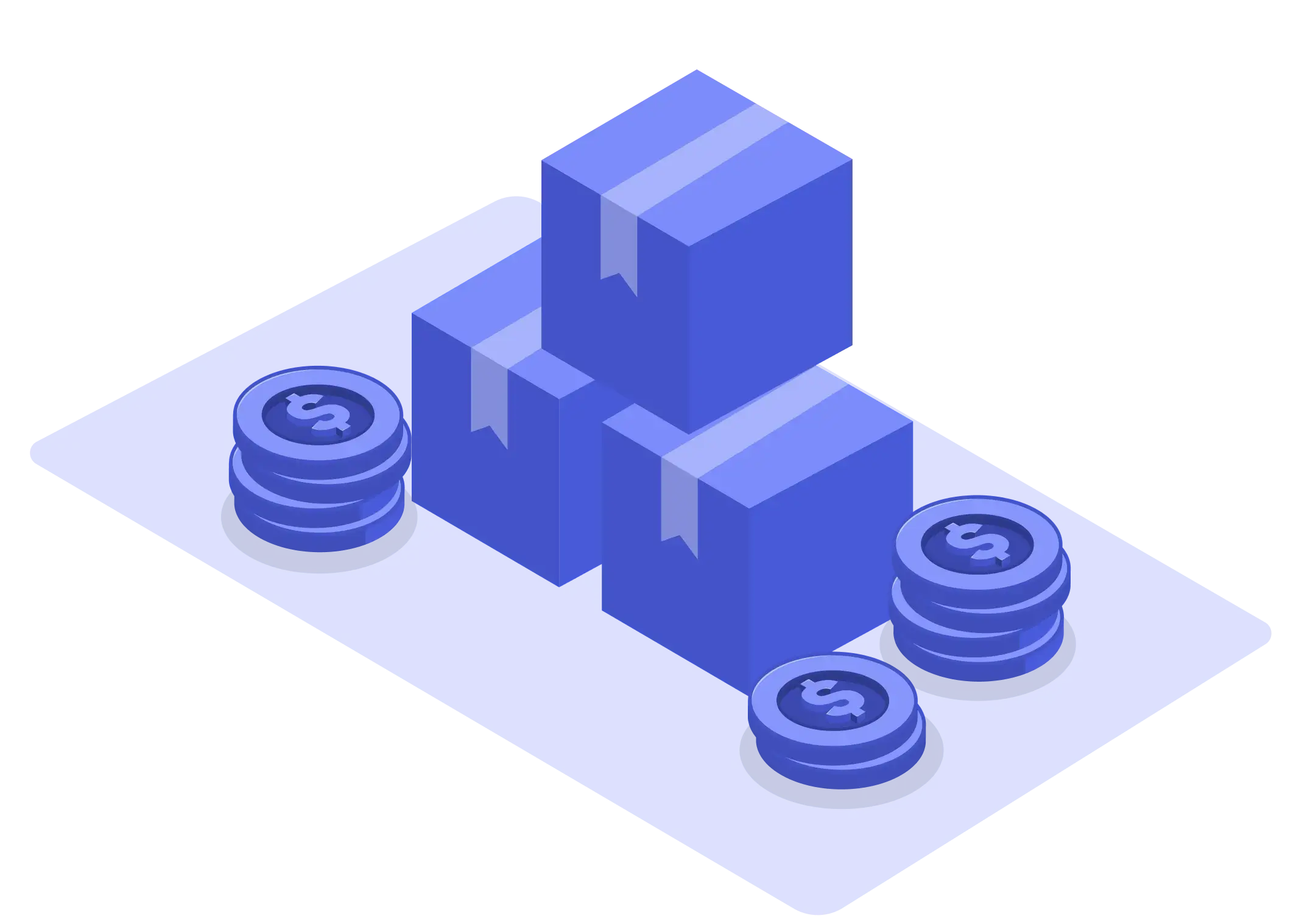
Table of Contents
How do companies work out the real costs of their amazing products before selling them? The purchase price is only one factor in determining real business product costs. At this point, Inventory Costing Methods emerge as the key solution. These methods serve as the secret sauce of cost accounting, which businesses use to calculate inventory value and the crucial Cost of goods sold (COGS).
Forget dry accounting jargons for a second. Imagine you’re running a cool coffee shop. Your coffee shop purchases beans at varying prices as the month progresses. What bean price determines your profit margin when you sell a latte? Inventory costing methods provide answers to this fundamental question. These methods go beyond simple calculations as they represent inventory cost strategies that significantly affect your financial standing.
What Are Inventory Costing Methods?
Inventory costing methods represent the different approaches businesses choose to allocate costs to their inventory. Inventory costing techniques enable companies to assess their stock value while it remains in storage or during customer transactions.
Why is this important? Your chosen inventory cost strategy affects both your profit margins and tax liabilities. In times of inflation, the choice between FIFO vs LIFO methods leads to significantly different financial outcomes. The LIFO method can produce highly variable outcomes in overall financial statements. To make sound financial decisions in your business you must learn to recognize these distinctions.
Why Accurate Inventory Valuation Matters
Financial Impact
Precise inventory value ensures accurate financial statements and helps determine genuine firm performance. It impacts critical business metrics:
- Balance sheet accuracy
- Cost of goods sold calculations
- Gross profit calculation
- Tax liability assessment
Strategic Benefits
Proper inventory costing enables businesses to:
- Make informed pricing decisions
- Optimize warehouse space utilization
- Evaluate supplier relationships
- Plan future inventory investments
Key Inventory Costing Methods
Selecting an appropriate inventory costing system presents the same level of complexity as finding one's way through a labyrinth. But don't worry—we've got your back, Jack! This section will analyze the top three methods for inventory valuation. The three main inventory valuation approaches include First-In-First-Out (FIFO), Last-In-First-Out (LIFO), and Weighted Average Cost (WAC). Through the examination of actual business cases this guide teaches you about each inventory method's performance together with its advantages and disadvantages.
First In, First Out (FIFO)
The FIFO cost accounting method remains the primary choice for industries that handle goods with expiration dates or that require rapid sales. This Cost accounting method approach mandates that inventory items bought earlier must be sold earlier.
Advantages of FIFO
- Accurate Reflection of Current Costs: FIFO offers a precise representation of profits during inflationary periods because it links older inventory costs to revenue.
- Simpler Inventory Management: FIFO matches natural stock rotation, which minimizes waste and spoilage, making it ideal for food and pharmaceutical industries.
- Higher Net Income: In inflationary times, FIFO accounting usually produces lower costs of goods sold along with elevated reported profits, which helps to increase investor confidence.
Limitations of FIFO
- Higher Tax Liability: Higher net income leads to increased tax payments that may affect cash flow.
- Mismatch in Pricing: Significant price increases can lead to FIFO generating inaccurate market condition reflections which results in potential pricing inefficiencies.
Example Calculation of FIFO
As a coffee shop owner, you bought beans at varying prices over time.
January: 100 units at $5 each
February: 100 units at $6 each
March: Sold 150 units
The cost of goods sold (COGS) is calculated using the FIFO methodology: (100 units × $5) + (50 units × $6), which equals $800.
The COGS using FIFO amounts to $800, calculated as (100 units × $5) + (50 units × $6), which is $500 added to $300.
The value of the remaining inventory depends on the latest unit purchase cost, which stands at $6 per unit.
Last In, First Out (LIFO)
The LIFO cost accounting method assumes businesses sell their newest inventory before older stock. LIFO remains a rare accounting method worldwide but has significant popularity in the United States due to tax benefits that emerge during periods of inflation.
Advantages of LIFO
- Lower Taxes During Inflation: LIFO decreases the taxable income by aligning recently higher inventory costs with sales revenue, which helps preserve the company's cash flow.
- Better Matching of Costs: Through LIFO, businesses can pair COGS with present market rates, which delivers a precise profitability picture during market volatility.
Limitations of LIFO
- Complexity: The LIFO methodology requires thorough inventory documentation, which International Financial Reporting Standards (IFRS) bans while Generally Accepted Accounting Principles (GAAP) accept it.
- Lower Reported Profits: This accounting method typically produces reduced PAT that can turn away prospective investors.
- Inventory Obsolescence Risk: Products that remain unsold for an extended period become obsolete or outdated.
Example Calculation of LIFO
Using the same coffee shop example:
January: 100 units at $5 each
February: 100 units at $6 each
March: Sold 150 units
Under LIFO accounting, the most recent inventory acquisitions are used first to compute the cost of goods sold.
(100 units × $6) + (50 units × $5) = $600 + $250 = $850
The remaining inventory value would reflect the older purchase price ($5 per unit).
Weighted Average Cost (WAC)
The Weighted Average Cost (WAC) inventory costing method approaches inventory valuation through an entirely distinct strategy. The system determines a weighted average cost for all similar items available for sale within a period rather than considering the purchase sequence. The Weighted Average Cost method serves businesses well when their products are uniform or when companies desire straightforward inventory valuation processes.
Advantages of WAC
- Simplicity: Because of its straightforward calculation process, this inventory costing method proves to be highly practical for businesses that produce homogeneous products.
- Smooth's Out Price Fluctuations: The weighted average cost method provides a consistent cost basis that reduces fluctuations in financial statements.
Limitations of WAC
- Less Accurate During Inflation: The weighted average cost method fails to reflect current market prices with the same precision as FIFO or LIFO methods do.
- Not Ideal for Unique Items: WAC works optimally for companies that sell similar products because it doesn't suit businesses with diverse and distinct inventory items.
How to Calculate WAC
- Total Cost of Inventory: Calculate the total purchase price by summing up the costs for all the units you bought.
- Total units available: Determine the overall inventory quantity by counting every available unit.
- Weighted Average Cost per Unit: The weighted average cost emerges from dividing the total cost by the total number of units.
- COGS: COGS is calculated by multiplying the number of units sold by their cost, which is computed using the weighted average technique.
Here’s the formula:
Weighted Average Cost = Total Cost of Goods Available ÷ Total Units Available
Using the same coffee example:
January: 100 pieces at $5 each ($500 total).
February: 100 units at $6 each ($600 total).
Total cost: $500 + $600 = $1,100.
Total units = 100 plus 100 = 200.
The weighted average cost computation yields $5.50 per unit, as $1,100 divided by 200 = $5.50.
Using the weighted average technique, the COGS for 150 units sold is $825.
150 × $5.50 = $825
Comparing Inventory Costing Methods
The inventory costing method you use should be in line with your business objectives, just as the instruments you use should. We’ve simplified your comparison of FIFO, LIFO, and Weighted Average Cost (WAC) by presenting them in an easy-to-read table format.
FIFO vs. LIFO vs. WAC: A Side-by-Side Comparison
Aspect | FIFO | LIFO | WAC |
---|---|---|---|
Definition | Assumes older inventory is sold first. | Assumes newer inventory is sold first. | Averages the cost of all inventory items. |
Best For | Perishable goods, industries with stable or rising prices. | Industries with rising costs, businesses looking to reduce taxable income. | Businesses with large volumes of similar products. |
Impact on COGS | Lower COGS during inflation (older, cheaper costs). | Higher COGS during inflation (newer, higher costs). | Moderate COGS, smooths out price fluctuations. |
Impact on Net Income | Higher net income during inflation. | Lower net income during inflation. | Balanced net income, less volatility. |
Tax Implications | May increase tax liability due to higher profits. | Reduces taxable income during inflation. | Moderate tax impact, less extreme than FIFO or LIFO. |
Inventory Valuation | The balance sheet reflects newer, higher-cost inventory. | Reflects older, lower-cost inventory on the balance sheet. | Averages all inventory expenses to achieve a balanced valuation. |
Ease of Use | Simple to understand, yet labor-intensive to track. | Complex to maintain, especially with frequent price fluctuations. | Simplifies inventory tracking at a reasonable cost. |
Financial Reporting | Higher profitability attracts investors. | Lower profitability means less taxable income. | Ensures consistent and stable financial reporting. |
Key Takeaways from the Comparison:
FIFO vs. LIFO:
- FIFO methods produce higher profit reports and work well for goods that expire quickly.
- LIFO acts as an effective tax-saving approach for industries experiencing rising costs.
FIFO vs. WAC:
- FIFO enables precise financial statements because it directly correlates inventory figures with the physical stock flow.
- The WAC approach streamlines computational processes making it perfect for companies manufacturing similar products.
LIFO vs. WAC:
- LIFO reduces taxable income but can be complex to manage.
- WAC provides a balanced approach and is easier to implement.
Which Method Should You Choose?
The best inventory costing method depends on your business’s unique needs:
- FIFO: Choose if you want to show higher profitability or deal with perishable goods.
- LIFO: Use this strategy if you are in a high-cost industry and want to save money on taxes.
- WAC: Choose this method when you need a simplified and consistent inventory valuation method for large volumes of related products.
A thorough understanding of inventory valuation methodologies enables you to make sound judgments that align with your company's strategic goals. Our following blog will demonstrate practical applications and guidance for successfully applying these cost accounting techniques.
Advanced Inventory Costing Techniques
Specific Identification Method
The Specific Identification Method is the highest requirement for organizations dealing with one-of-a-kind or custom premium goods. Rather than categorizing products, this system notes the exact cost of each individual item.
Key features:
Precision: This method compares the real cost of each sold item to the produced revenue.
Best for: The Specific Identification Method is most suited for tracking premium commodities, real estate holdings, high-end vehicles, and unique products.
Pros:
Ensures high accuracy in financial reporting.
Companies that sell products with unique values should use this strategy.
Cons: This method is inefficient for dealing with h
The Retail Inventory Method
Retailers can use the Retail Inventory Method to quickly and accurately assess the worth of their inventory. Rather than completing real physical counts, the Retail Inventory Method uses cost-to-retail ratios to calculate ending inventory levels.
Key features:
Estimation Power: The calculation of inventory value is based on the examination of sales data and markup percentages.
The Retail Inventory Method is best suited for department stores, which manage enormous product amounts and constantly modify prices.
Pros:
The technology simplifies inventory management and reduces the need for frequent physical counts.
Suitable for interim financial reporting.
Cons:
This methodology is less accurate than other ways as it relies on assumed figures.
This strategy does not work well with organizations that use very volatile pricing tactics.
Moving Average Cost
The Moving Average Cost method recalculates inventory costs with each new purchase to provide a dynamic substitute for the Weighted Average Cost system. Industries that operate under perpetual inventory systems commonly use this technique.
Key features:
Key features include dynamic updates, which recalculate the average cost per unit after each transaction.
This technique is ideal for organizations that have a constant flow of inventory in and out of their storage (for example, e-commerce and manufacturing).
Pros:
Real-time pricing smoothing ensures consistency in COGS and inventory assessments.
It works perfectly with automated inventory management systems.
Cons:
Requires dependable software for regular calculations.
Under times of significant market volatility, firms may discover that FIFO or LIFO procedures give superior recording accuracy than alternative methods.
Final Thoughts
Selecting the appropriate inventory costing method enables businesses to reach their full potential beyond simply performing calculations. Whether you’re team FIFO, team LIFO, or team WAC, the goal is the same: Your ability to refine inventory valuation methods will lead to better decisions based on data analysis.
Without the right implementation tools, your cost accounting methods will never reach their full potential. At this point, the Omniful Inventory Management System becomes essential. Through real-time tracking capabilities and advanced reporting features, Omniful eliminates the guesswork in managing inventory. Omniful can transform your inventory game. Your business demands an inventory management system that delivers more than standard performance. Get a free demo today!