Returns Consolidation: Collecting Returns at Regional Depots Before Shipping to Main Warehouse
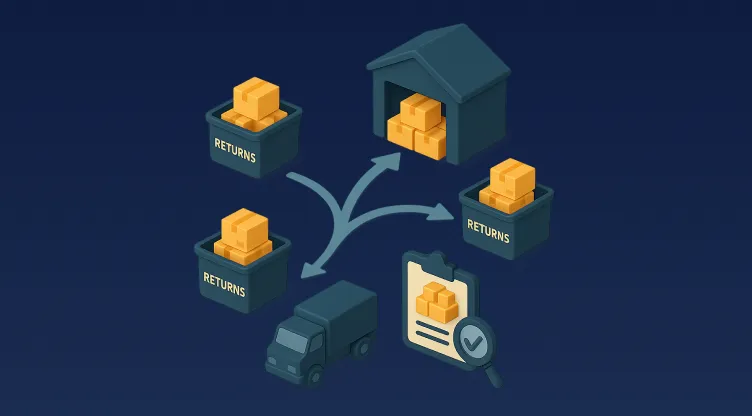
Table of Contents
Skim-and-Win: The Regional Returns Advantage
- Consolidating returns at regional depots cuts transportation costs.
- It improves tracking, sorting, and inspection before items hit HQ.
- Boosts operational efficiency and streamlines reverse logistics.
- Vital for omnichannel and cross-border MENA businesses.
- Supports return flows from physical stores, last-mile drop-offs, and doorstep pickups.
- Enables automation, quality grading, and data-driven improvements.
- Requires robust Returns Management and Warehouse Systems.
- Aligns with MENA customer expectations of fast refunds and hassle-free processes.
- Key tech enablers include geofencing, TMS routing, barcode scanning, and item-level tracking.
Returns Are No Longer a Cost Centre — They're Strategic
In the age of e-commerce growth, reverse logistics has moved to the front lines of retail strategy. In the MENA region, customer expectations around easy returns are rising just as businesses face mounting pressure to reduce operational costs.
A powerful way to strike this balance is returns consolidation — collecting return items at regional depots before routing them to the main warehouse.
This approach saves money, improves return accuracy, and enhances customer satisfaction. It’s especially effective for companies operating across large geographies like Saudi Arabia, UAE, Egypt, and beyond.
Let’s unpack why this model is redefining modern returns management.
Understanding Returns Consolidation in Logistics
Returns consolidation involves aggregating returned items from various channels — doorstep pickups, retail stores, last-mile partners — into local or regional depots. Once a bulk threshold is reached, these items are transferred to the central warehouse.
This approach differs from direct returns, where every item is sent individually back to HQ.
Why It Matters
Without consolidation, reverse logistics becomes:
- Expensive: More vehicles and fuel are used per return.
- Disorganised: Items arrive unsorted, delaying processing.
- Inaccurate: Higher chances of loss or misrouting.
With consolidation, operations become lean, centralised, and data-rich.
Reverse Logistics in the MENA Context
MENA countries span vast distances, especially in KSA and Egypt. Many retailers also manage both online and offline sales, creating complex return pathways.
Regional Complexities
- Long delivery routes across Riyadh, Jeddah, Dammam, or between Cairo and Alexandria.
- Omnichannel presence: Online sales, in-store purchases, and social commerce all generate returns.
- Regulatory requirements like ZATCA compliance or proof of delivery.
- High return expectations from shoppers on platforms like Noon, Amazon, and Namshi.
In this environment, direct-to-warehouse returns are inefficient and costly. Consolidation becomes not only smarter, but necessary.
Benefits of Returns Consolidation at Regional Depots
1. Lower Transportation Costs
- Reduces the number of trips between the field and the main DC.
- Optimises vehicle load by batching returns.
2. Faster Return Processing
- Inspections and grading can begin at regional hubs.
- Items are scanned and categorised before they arrive at HQ.
3. Improved Inventory Accuracy
- Using systems like Inventory Management, SKUs can be marked as in-return, available-for-restock, or pending disposal.
4. Customer Satisfaction
- Customers receive faster refunds.
- Better communication via return tracking APIs.
5. Better Route Planning
- TMS systems can cluster return pickups by zone and load.
- Reduces environmental impact.
What a Returns Depot Looks Like in Action
Step 1: Multi-Channel Return Creation
Returns can come from:
- Buy Online, Return In Store (BORIS)
- Reverse pickups from customers’ homes
- Failed deliveries sent back from the last-mile fleet
- Drop-offs at designated retail outlets
Step 2: Arrival at Regional Depot
Each item is:
- Scanned using a barcode reader
- Logged into a Returns Management system
- Grouped by category, condition, or vendor
- Tagged with RMA (Return Merchandise Authorisation)
Step 3: Sorting & Inspection
Items undergo:
- Physical inspection
- Grading (sellable, repair, recycle)
- Packaging for consolidation
Step 4: Bulk Shipment to HQ
Once the threshold is met:
- The TMS triggers a return-to-warehouse job.
- Items are loaded in optimised clusters.
- Drivers use route optimisation tools to minimise travel time.
Technology Solutions That Make It Work
To make regional returns work, your operations need the right tech backbone:
1. Returns Management System
A platform like Omniful's Returns Module allows:
- Real-time tracking of returns
- Item-level return status (picked up, scanned, in transit)
- Integration with ecommerce platforms for refunds and updates
2. Warehouse Management System (WMS)
Essential for:
- Creating dedicated zones for return items
- Tracking SKU freshness, damage, or expiration
- Triggering auto-restocking or write-offs
3. Transportation Management System (TMS)
It supports:
- Clustering return trips
- Managing vehicle load and capacity
- Triggering driver cash collection for COD returns
- Creating AWB and return labels
4. Barcode and Mobile Scanning
Drivers and depot workers can scan return items using mobile devices, ensuring accurate logging.
5. APIs for Return Updates
Omniful’s open APIs connect with platforms like Shopify, Zid, or Salla to:
- Update return status
- Trigger automated refunds
- Notify customers in real-time
MENA Success Story: Optimising Reverse Logistics
Case: A Major Fragrance Retailer in Riyadh
The client faced:
- High costs in reverse deliveries
- Poor visibility into return items
- Delays in restocking sellable returns
Solution: By deploying regional depots in Riyadh, Dammam, and Jeddah, and connecting them through Omniful’s Returns and TMS modules, the retailer achieved:
- 40% cost reduction in reverse deliveries
- 2x faster return cycle time
- Better customer satisfaction and fewer complaints
Returns Consolidation and Quick-Commerce
For grocery, pharma, or Q-Commerce operations, returns often involve perishable or time-sensitive goods. Consolidation helps in:
- Isolating faulty or expired items before reaching the warehouse
- Creating audit trails to ensure compliance
- Speeding up replenishment in local hubs
It’s also perfect for businesses running dark stores or micro-fulfilment centres across KSA and UAE.
Challenges to Watch Out For
Returns consolidation is powerful, but needs careful planning.
- Hub capacity: Ensure depots have enough space for sorting returns.
- Technology readiness: Invest in connected, modular platforms.
- Staff training: Depot workers must follow grading protocols accurately.
- Fraud control: Use item serialisation to prevent bogus returns.
Take Action: Automate Returns, Delight Customers
Returns don’t have to be a headache.
With the right Returns Management, WMS, and TMS infrastructure, you can:
- Slash costs
- Improve turnaround times
- Create a competitive edge
Omniful enables businesses across MENA to set up returns depots, track item conditions, and ship in bulk with precision.
Frequently Asked Questions
What is reverse logistics in simple terms?
It refers to moving goods from the customer back to the seller or manufacturer for returns, repairs, or recycling.
Why is returns management important?
Efficient returns build trust, reduce costs, and maintain stock accuracy.
Can regional returns reduce transportation costs?
Yes. Batching returns into regional depots reduces fuel use, trip frequency, and manpower.
What technology supports returns consolidation?
Tools like Omniful’s Returns System, mobile scanners, and TMS platforms enable smooth operations.
Do returns depots work for small businesses?
Yes, especially if they operate in multiple cities or regions. Omniful offers scalable solutions for all sizes.