WMS-Integrated Pick-to-Light & Voice Picking: Minimising Search Time and Boosting Speed
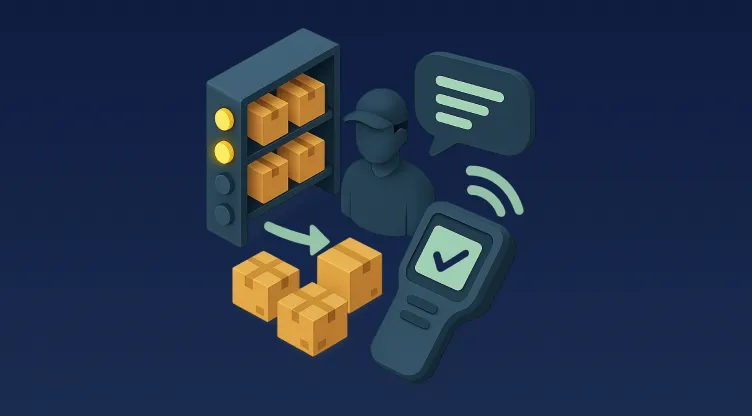
Table of Contents
Making the Warehouse Talk and Light the Way to Faster Fulfilment
In today’s fast-paced supply chain, speed is currency. Whether fulfilling Q-Commerce orders in Riyadh or preparing retail inventory for Dubai Mall, warehouse efficiency directly impacts customer satisfaction and revenue.
Yet many operations still rely on outdated picking processes that slow workers down.
The solution? Pick-to-Light and Voice Picking technologies integrated into a modern Warehouse Management System (WMS).
These tools dramatically reduce labour costs, eliminate search time, and boost accuracy—especially when used in multi-lingual, high-velocity warehouses across the MENA region.
Quick Bytes for Busy Minds
- Pick-to-Light guides workers using LED displays for quick SKU location.
- Voice Picking provides hands-free, spoken instructions to reduce delays.
- Integrated WMS coordinates real-time inventory, zones, and pick routes.
- These systems improve productivity by over 30% in busy warehouses.
- Ideal for MENA operations handling high SKU volume with multilingual staff.
- Tools like Omniful WMS support seamless Pick-to-Light and Voice Picking integration.
Why Traditional Picking Slows You Down
In many MENA warehouses, workers still rely on:
- Printed pick lists
- Manual zone search
- Visual stock checks
- Paper-based bin confirmations
This process is slow, labour-intensive, and error-prone. During peak times like Ramadan, Black Friday, or Back-to-School promotions, delays in picking result in:
- Missed delivery windows
- Customer dissatisfaction
- Inventory mismatches
- Excessive returns
Digital transformation in warehouses must start with how labour interacts with inventory—and that begins at the picking stage.
Understanding Pick-to-Light: Visibility Means Velocity
Pick-to-Light (PTL) systems use light indicators and digital displays mounted on storage racks or shelving bins.
How It Works:
- Worker scans the order or tote.
- Light modules on the correct bins flash.
- Digital display shows the quantity to pick.
- Worker confirms by pressing a button or scanning a code.
Key Benefits:
- No time wasted searching for SKUs.
- Ideal for high-volume and batch picking.
- Suitable for visually-oriented environments with fast-moving staff.
- Reduces picking errors by over 50%.
In a Riyadh warehouse managing e-commerce apparel, Pick-to-Light slashed average pick times by 37% after integration with Omniful’s WMS.
Voice Picking: The Warehouse Speaks to Your Staff
Voice Picking uses a headset and speech recognition software to guide pickers verbally through their tasks.
Typical Voice Picking Workflow:
- Picker logs in via headset.
- System announces the next location and quantity.
- Picker confirms each action verbally.
- System proceeds to the next task.
Advantages for MENA Warehouses:
- Hands-free operation for picking, lifting, and scanning.
- Multilingual capabilities for Arabic, English, Urdu, and more.
- Less screen time means better focus on movement and safety.
- Ideal for large warehouses where mobility is key.
Voice Picking improves both labour productivity and staff morale, especially for workers new to the warehouse layout or language.
Why WMS Integration Is Critical
Without WMS integration, Pick-to-Light and Voice Picking operate in silos. That limits their full potential.
With integration into Omniful’s Warehouse Management System, these systems benefit from:
- Real-time inventory updates
- Zone-based task allocation
- Intelligent order batching
- Automated re-slotting suggestions
- Error flagging and correction prompts
WMS acts as the brain—coordinating pick flow, validating every action, and ensuring data integrity.
Comparing Pick-to-Light vs. Voice Picking
Feature | Pick-to-Light | Voice Picking |
---|---|---|
Ideal for | High-volume, low SKU warehouses | Large warehouses with wide SKU ranges |
Labour type | Visual, hands-on tasks | Hands-free, mobile tasks |
Language dependency | Minimal | Multilingual speech required |
Speed boost | ~30–40% | ~20–35% |
Integration complexity | Moderate | High (requires audio calibration) |
Training time | 1–2 days | 2–3 days |
MENA operations can combine both systems, using Pick-to-Light in dense zones (e.g., accessories) and Voice Picking in large product areas (e.g., electronics or bulk goods).
Labour Challenges Solved by Pick-to-Light and Voice Picking
Warehouse managers across Saudi Arabia, UAE, and Egypt often struggle with:
- High turnover during seasonal periods
- Multilingual teams
- Training costs
- Low pick accuracy
- Worker fatigue
Pick-to-Light and Voice Picking address these by:
- Reducing mental strain from searching
- Offering visual/audio guidance without language barriers
- Accelerating new worker training
- Increasing pick rate without compromising accuracy
Labour becomes more productive and less stressed—translating to better performance during peak demand periods.
Real-World Use Case: Omniful WMS + Pick-to-Light in Dubai
Business Type: Fashion fulfilment centre for 5 online brands
Challenge: Slow picking, high seasonal turnover
Solution: Deployed Omniful WMS with Pick-to-Light in 3 zones
Results:
- Training time cut by 60%
- Average pick time reduced from 18s to 10s
- Pick error rate dropped below 1%
- Temporary workers reached productivity in under 2 shifts
Integrated dashboards showed real-time performance by worker and zone—allowing better labour planning and shift rotation.
Reducing Labour Costs Without Cutting Corners
Warehouse wages in GCC countries are rising. Yet efficiency doesn’t require hiring more—it requires using technology smarter.
Here’s how WMS-integrated picking systems reduce cost:
- Fewer errors = lower returns
- Faster picking = more orders per shift
- Simpler training = less onboarding cost
- Higher morale = less turnover
Investing in tools like Pick-to-Light and Voice Picking pays off within 2–4 quarters, depending on your order volume.
Compatibility with Other Systems
Your warehouse should operate as one ecosystem. Omniful ensures your picking tech works with:
- Inventory Management: Ensures stock visibility in real time.
- Order Management System: Allocates pick tasks based on order priority.
- Shipping Gateway: Syncs with dispatch teams after packing.
- Returns Management: Reintegrates returns into pickable inventory.
Unified systems = fewer bottlenecks, better throughput.
KPIs to Monitor After Deployment
Track these to evaluate success:
- Pick time per SKU
- Training hours per seasonal worker
- Order fulfilment rate
- Pick accuracy rate
- Worker retention during peak months
- Orders fulfilled per labour hour
Omniful provides these metrics via dashboard tiles—no extra configuration required.
Mistakes to Avoid
Even advanced tech can fail if used poorly. Avoid:
- Ignoring layout mapping—make sure pick zones match voice/light logic
- Not investing in mobile infrastructure (Wi-Fi, power backups)
- Rushing training sessions
- Over-complicating SKU assignments
- Failing to analyse post-implementation KPIs
Proper deployment is just as important as the tech itself.
Preparing for the Future: AI-Powered Picking
As warehouses move towards predictive logistics, AI will:
- Recommend pick paths dynamically
- Adjust voice commands based on user pace
- Suggest staffing changes by shift
- Predict mispicks before they occur
These features will only work with integrated systems. That’s why starting with Omniful’s modular WMS today prepares you for tomorrow’s AI-driven warehouse.
Light the Path to Faster Fulfilment
📦 Upgrade to Omniful WMS with Pick-to-Light Support
📊 Book Your Demo Now
FAQs
What is Pick-to-Light in a warehouse?
It’s a system that uses light indicators to guide workers to the correct bin or shelf for picking, improving speed and accuracy.
How does Voice Picking help reduce labour costs?
It allows hands-free operation, faster movement, and less reliance on visual scanning—making staff more efficient.
Can both systems run in the same warehouse?
Yes. Many warehouses use Pick-to-Light in dense zones and Voice Picking in wide, mobile-heavy areas.
Does this require a new WMS?
Not necessarily. But using a WMS like Omniful allows better integration, real-time syncing, and performance tracking.
Is this suitable for temporary workers or non-English speakers?
Yes. Both systems can be configured in multiple languages and are ideal for fast onboarding.