Efficient Warehouse Management for Multinational Operations: Your Complete Guide
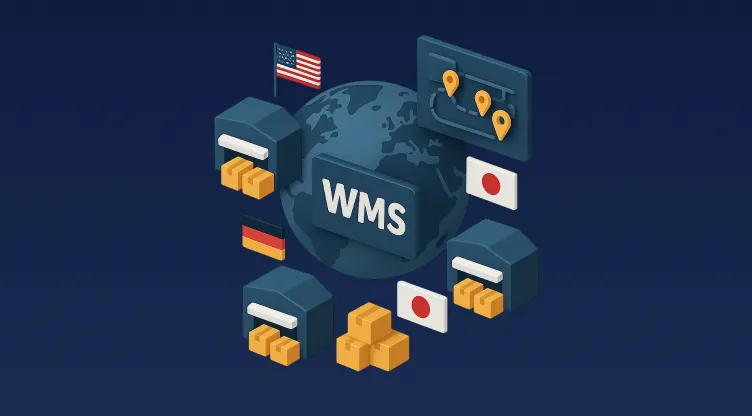
Table of Contents
Quick Overview – Key Steps for Global Warehouse Success
-
Managing warehouses globally demands precise stock tracking and efficient workflows.
-
Cross-border operations require accurate, real-time data and strong compliance.
-
Advanced WMS systems reduce costs, improve order accuracy, and streamline processes.
-
Omniful’s WMS offers multi-hub support, real-time tracking, and automated workflows.
Introduction: Why Multinational Warehouse Management is Challenging
Operating warehouses across multiple countries presents unique challenges. These include managing inventory in real time, handling cross-border logistics, and complying with diverse regulations. Without the right systems, businesses can face delays, increased costs, and unhappy customers.
A robust Warehouse Management System (WMS) solves these issues. It provides real-time data, reduces manual work, and improves overall efficiency. This leads to faster order processing, better stock control, and smoother global operations.
For example, Omniful's Warehouse Management System is built for businesses with global reach. It offers real-time stock visibility, automated workflows, and seamless integrations, making it ideal for complex, multinational operations.
Key Challenges in Multinational Warehouse Management
1. Keeping Track of Inventory Across Locations
Managing stock in multiple countries can be difficult. Without accurate data, businesses risk overstocking, stockouts, and missed sales. An effective WMS addresses these problems by providing:
-
Real-Time Stock Visibility: Monitor stock across different locations, reducing errors and delays.
-
Multi-Hub Management: Track inventory in real time for better order accuracy.
-
Batch and Lot Tracking: Group items for better quality control and traceability.
-
Item Serialization: Use unique IDs for precise item tracking, reducing picking errors.
Example: A retailer with warehouses in Dubai, Riyadh, and Cairo can use real-time stock tracking to avoid overselling and improve customer satisfaction.
For better control over stock, integrating an Inventory Management System (IMS) can help maintain accurate stock levels.
2. Handling Diverse Compliance Requirements
Different countries have unique rules for product labeling, taxes, and customs. Failing to comply can lead to fines, shipment delays, or reputational damage. A WMS designed for global use can simplify this by:
-
Automating Invoicing and Labeling: Generate accurate documents for different regions, reducing compliance risks.
-
Multi-Language and Currency Support: Handle local languages and currencies for better customer experiences.
-
Batch and Lot Control: Track items in batches, ensuring quality and regulatory compliance.
Example: A company selling electronics in the MENA region can use batch tracking to meet local quality standards, reducing returns and building customer trust.
For better return handling, consider integrating a Returns Management System to streamline the process.
3. Managing Cross-Border Shipping and Logistics
Shipping goods internationally is more than just moving items. It involves customs paperwork, multiple carriers, and real-time tracking. An effective WMS can simplify this by:
-
Carrier Integration: Connect with multiple shipping providers for faster deliveries.
-
Automated Waybill (AWB) Generation: Create accurate shipping labels to reduce customs delays.
-
Real-Time Order Visibility: Track orders from warehouse to customer for better service.
Example: A fashion retailer shipping products from Europe to the Middle East can automate customs paperwork, reducing delays and improving customer satisfaction.
For seamless cross-border shipping, integrating a Shipping Gateway can reduce costs and improve accuracy.
4. Controlling High Operational Costs and Scaling Challenges
Running global warehouses can be expensive. Labour, storage, and transportation costs can add up quickly. A scalable WMS reduces these expenses by automating routine processes:
-
Optimized Picking Paths: Use AI to reduce travel time, cutting labour costs.
-
Automated Workflows: Automate tasks like stock counting, improving accuracy and speed.
-
Data-Driven Decisions: Use real-time analytics for smarter, cost-effective business choices.
Example: An e-commerce business using Omniful’s WMS can reduce picking time by 30%, resulting in faster order processing and lower labour costs.
For businesses looking to improve overall efficiency, integrating an Order Management System (OMS) can help streamline the entire order lifecycle.
Why Choose Omniful’s WMS for Multinational Operations?
Omniful’s WMS is built for businesses operating in multiple countries. It offers:
-
Multi-Location Support: Manage stock across different countries with real-time insights.
-
Automated Order Routing: Ensure the right product reaches the right customer quickly.
-
Robust Data Security: Protect sensitive information with advanced security protocols.
-
Seamless Integrations: Connect with TMS, Plug and Play Integrations, and sales channels for unified operations.
-
Scalable Infrastructure: Grow your business without worrying about system limitations.
Best Practices for Efficient Global Warehouse Management
-
Centralize Data Management: Use a single WMS for consistent, real-time stock visibility.
-
Automate Replenishment: Set stock thresholds to avoid shortages and overstocking.
-
Leverage Predictive Analytics: Use data to forecast demand and optimize stock levels.
-
Integrate Seamlessly: Connect your WMS with order and transport systems for full control.
-
Focus on Customer Experience: Use real-time tracking and automated alerts to keep customers informed.
FAQs – Multinational Warehouse Management
Q1. What is a Warehouse Management System (WMS)?
A WMS is software that manages warehouse operations, including inventory control, order processing, and shipping.
Q2. Why is real-time inventory important in global operations?
Real-time data reduces stockouts, minimizes delays, and improves customer satisfaction.
Q3. How can Omniful’s WMS support cross-border logistics?
It integrates with multiple carriers, automates customs paperwork, and offers real-time tracking.
Q4. How do WMS systems handle regional compliance?
Omniful’s WMS automates invoice generation, batch tracking, and multi-barcode support.
Q5. Can I use Omniful’s WMS for different warehouse types?
Yes, it supports dark stores, retail outlets, and large distribution centres.