Multi-Warehouse Operations: Advanced Techniques & Strategies
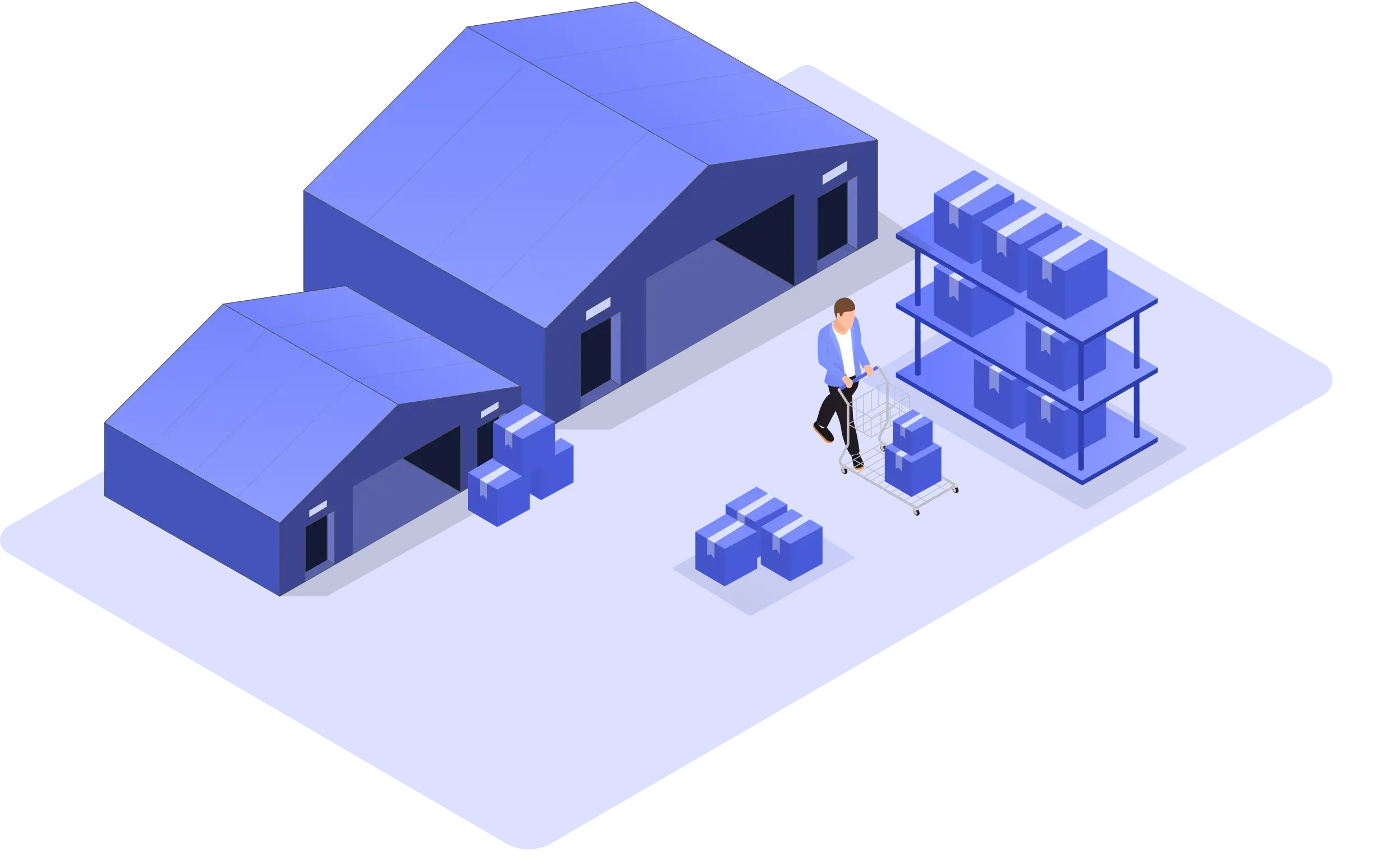
Table of Contents
In our earlier blog post, we examined the benefits and difficulties of Warehouse inventory management for multiple warehouse operations. We first recognized the challenges inherent in operating a logistics network across multiple locations before investigating how strategically positioned warehouses can enhance supply chain efficiency and deliver better customer experiences. A deep understanding of basic principles does not meet the requirements of the present cutthroat corporate environment.
Businesses that want to succeed in warehouse management must go beyond the basics and embrace innovative ideas and approaches. This article explores advanced techniques along with sophisticated Multi-location logistics strategies and offers practical advice to help you maximize your multi-warehouse network, simplify your operations, and fine-tune warehouse inventory control.
Strategies to Streamline Multi-Warehouse Operations
Successful multi-warehouse management requires much more than creating additional storage zones. You must use a strategic, data-oriented method integrating advanced techniques to enhance all parts of your multi-site operations. Now, we'll examine major techniques that can improve operational efficiency and streamline processes.
Leveraging Automation and Technology
In the Industry 4.0 age, efficient multiple warehouse management depends on automation and technology as basic needs. By means of automation, companies eliminate human errors, speed up processes, focus on supply chain optimization, and free their employees to commit time for critical tasks. Companies can use these developments as follows:
- Implement Robust Inventory Management Software: To achieve real-time inventory tracking at all sites you need a centralized Warehouse Management System (WMS). The system requires connections with RFID tags and barcode scanners as well as IoT devices to enable precise stock movement tracking while reducing human errors.
- Automate Repetitive Tasks: Automation enhances operational efficiency by taking over repetitive functions such as item picking and packing together with inventory management tasks. The use of autonomous mobile robots (AMRs), automated guided vehicles (AGVs), and voice-picking systems enables businesses to optimize their operations while lowering labor expenses and improving accuracy.
- Use Data Analytics for Decision-Making: Businesses can use data analytics to predict demand patterns and optimize their inventory while identifying operational inefficiencies. The data-driven approach facilitates efficient stock allocation and minimizes the risks associated with overstocking and stockouts.
Enhancing Communication Between Warehouses
The practice of operating in silos hinders operational efficiency, more so when multiple logistics locations are involved. The absence of clear and consistent communication between warehouses results in perfectly crafted plans becoming ineffective. Here are strategies to enhance communication:
- Centralize Data Access: Centralized access to data allows every warehouse to operate using the same real-time information. This approach decreases discrepancies and enhances collaborative efforts.
- Establish Clear Communication Protocols: Combining internal communication platforms with electronic notification systems and shared databases creates seamless information exchange capabilities. Operation coordination improves when well-defined protocols eliminate misunderstandings and prevent operational delays.
- Utilize Modern Communication Tools: Modern communication tools, such as instant messaging and video conferencing, help teams maintain connectivity in large or dispersed warehouses. Contemporary communication solutions also enable users who move between locations to deliver urgent messages instantly and without delay.
Developing an Effective Distribution Plan
Even though your warehouses maintain maximum stock levels, they will fail to deliver products effectively to customers without a robust distribution strategy. Multi-location logistics requires supply chain optimization through a well-developed distribution plan:
- Strategic Warehouse Location: Warehouses should be strategically located to reduce transportation time and expenses. This includes examining market demand, transit routes, and proximity to key clients.
- Optimize Order Management: Install systems that can handle orders across numerous locations, ensuring that orders are fulfilled from the most appropriate warehouse depending on inventory levels, shipping costs, and delivery schedules.
- Automate Replenishment and Stock Transfers: When inventory levels fall below a specific threshold, automated systems can generate replenishment orders, ensuring that products are always available for client orders. This includes automatic stock transfers between warehouses to keep inventory balanced.
- Implement Lean procedures: Simplify procedures by picking directly into shipping containers, eliminating needless handling and increasing order fulfillment efficiency.
Advanced Techniques for Warehouse Optimization
If you want to improve your Multiple Warehouse Management strategy, think big—and smarter. Warehouse optimization is more than just organizing shelves and tracking inventory; it's about using clever ways to turn your warehouses into efficient engines.
Dynamic Inventory Reallocation
Consider your warehouses automatically correcting inventory imbalances before humans ever notice. Dynamic inventory reallocation is a game changer in multiple warehouse management, using AI-powered technologies to reroute stock in real time, depending on changing demand.
- Automated Balancing: When regional demand spikes, systems like Omniful's predictive analytics initiate stock transfers between warehouses—for example, ice cream shipments before a heatwave. No more dead stock in cold climates!
- Hybrid Reallocation: Combining automatic and human processes (as shown in Dynamics 365) allows personnel to override AI recommendations amid supply chain disruptions.
- Risk Mitigation: Real-time tracking using warehouse inventory management software (such as Omniful) reduces overstocking by allocating extra goods to high-turnover hubs.
Pro Tip: Use multi-location logistics platforms with auto-replenishment rules to turn warehouses into a self-healing network.
Integration with Supply Chain Partners
The supply chain optimization process functions as a relay race rather than an individual sport. Create connections between your multi-warehouse management ecosystem and your business partners through:
- EDI & API: SAP's ecosystem integration uses electronic data exchange (EDI) to synchronize orders, shipments, and inventory data with suppliers in real-time. APIs automate operations such as order confirmations, reducing manual errors by 70 percent.
- Cloud-based Command Centres: Cloud-based command centers centralize data from warehouses, carriers, and suppliers, allowing for collaborative forecasting. For example, a shop may exchange real-time sales data with manufacturers in order to pre-stock seasonal inventories.
- Unified WMS: WMS unifies order management, transportation, and analytics into a single dashboard, allowing partners such as 3PLs and vendors to view real-time stock levels. Result? Faster restocks, fewer stockouts, and lower logistics expenses.
Using Data Analytics for Forecasting
Data analytics takes warehouse inventory management from reactive guesswork to proactive strategy. Here's how.
- Predictive Power: Omniful and other demand forecasting tools use historical sales data, weather data, and market trends. For example, a fashion brand employs artificial intelligence to estimate regional demand for winter coats, resulting in a 40% reduction in overstock.
- Safety Stock Smarts: Using probabilistic algorithms, calculate ideal safety stock levels to ensure warehouses buffer against supply chain disruptions without increasing expenses.
- Hyper-Local Forecasting: You can allocate inventories using ZIP code-level purchasing patterns. For example, there would be more sunscreen in Miami warehouses than in Minneapolis before summer.
Common Mistakes to Avoid in Multi-Warehouse Management
Multiple Warehouse Management solutions that start with good intentions often fail due to avoidable mistakes. Errors that include ignoring unique needs and creating overly complex workflows disrupt warehouse inventory management and cause problems across multi-location logistics. Remember that awareness is the initial step toward preventing major disasters. We will examine widespread mistakes and their respective avoidance strategies.
Neglecting Warehouse-Specific Demand
Ignoring the particular demand patterns of every warehouse is one of the most obvious mistakes in Multiple Warehouse Management or multi-location logistics. While centralized inventory control provides consistency, it can ignore the unique requirements of many sites, resulting in:
- Overstocking: Holding extra inventory in one warehouse while another causes stockouts, therefore tying down cash and raising holding costs.
- Stockouts: Underestimating demand in particular areas, stockouts lead to unmet orders and unhappy consumers.
Solution: Apply demand forecasting techniques considering local market dynamics, seasonal trends, and geographical variances. Predictive analytics will help you match inventory levels with expected demand so that every warehouse has just what it needs right now.
Failing to Use Real-Time Inventory Tracking
Manual inventory systems such as paper logs and spreadsheet records often produce human errors, which result in outdated data that causes numerous operational issues.
- Inaccurate Inventory Counts: Incorrect data entry or delayed inventory updates create mismatches between actual stock quantities and recorded information, which leads to both overstock situations and stock shortages.
- Inefficient Replenishment: Due to a lack of real-time data, replenishment orders are based on erroneous inventory readings, resulting in overstocking or lost sales opportunities.
Solution: Focus on real-time inventory tracking systems. Use barcode or RFID technology to automate data collecting, providing real-time stock-level visibility across many locations. Maintaining updated inventory data reduces errors and improves market demand responsiveness.
Overcomplicating the Workflow
Overly complex workflows can lead to miscommunication, mismanagement, or errors in inventory, order fulfillment, and forecasting. This can result in:
- Redundancy: Accidental repetition of operations, increasing labor costs and time spent on tasks.
- Inefficient Picking: Inefficient picking paths or methods can increase labor costs and supply chain cycle times.
- Inventory Damage: Items might be damaged during inter-warehouse stock movements if they are not properly documented and tracked.
Solution: Streamline workflows:
- Automating processes: Use current warehouse execution systems (WES) to automate redundancy-prone operations, such as order picking.
- Simplified Picking Methods: Use batch picking, zone picking, or wave picking to reduce travel time and improve accuracy.
- Clear Communication: Use inventory management software that includes communication tools to enable real-time communication and work assignment among employees.
Final Thoughts
It takes more than just piling boxes and crossing your fingers in Multiple Warehouse Management. Every single stock-keeping unit (SKU), shipment, and software decision is like a high-stakes chess move that can lead to huge wins or crushing losses due to stockouts and delays. You have all the plans, all the tech tricks, and the playbook for avoiding pitfalls. We must now carry out our plan.
The worst part, though, is that without the proper resources, even the most brilliant plans fail. In this situation, Omniful steps in like a code-clad supply chain superhero Our plug-and-play WMS does more than just streamline warehouse inventory management; it transforms multi-location logistics into a profit-generating, customer-pleasing, competitor-crushing juggernaut. Real-time data? Check. Is automation so smooth that it makes your head spin? Double-check.
So, what will it be? Keep fumbling with spreadsheets and guessing, or contact Omniful today to transform your warehouses into the nimble, unstoppable powerhouse they were designed to be. (Spoiler: Your future self will give you a high-five. What about the competition? Not very lot.)