End-to-End Supply Chain Visibility Tools: Total Transparency from Supplier to Customer
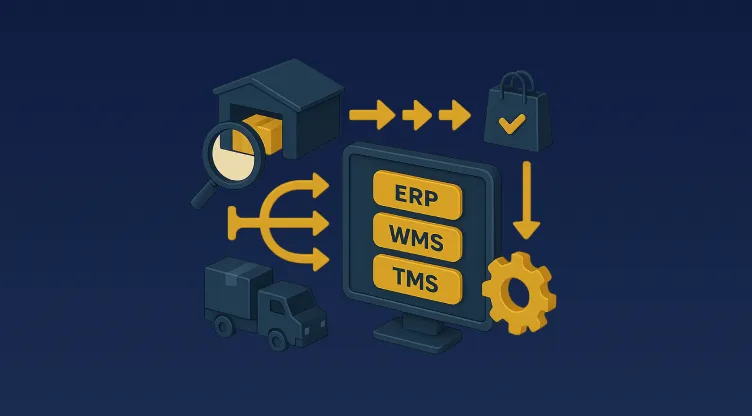
Table of Contents
Highlights at a Glance: Your Operational Advantage
- Full supply chain transparency transforms guesswork into data-backed decision-making.
- Businesses with poor visibility face operational delays, missed SLAs, and inventory inaccuracies.
- Leading logistics platforms today integrate multiple systems to offer live updates at every stage—from procurement to doorstep delivery.
- MENA-based companies require tailored visibility solutions due to cross-border logistics, regional infrastructure, and consumer behaviour.
- Modern visibility software empowers not just tracking—but real-time optimisation.
The Evolution of Visibility in Supply Chain Operations
Supply chain management was once viewed as a backend process—silent, necessary, and mostly hidden from customer view. That’s no longer the case. In today’s global and interconnected markets, visibility has become a strategic asset.
In fast-paced markets like the UAE, Saudi Arabia, and Egypt, consumers now demand precise delivery windows, real-time updates, and instant issue resolution. Behind these expectations lies one operational prerequisite: the ability to see and respond to every moving piece in the supply chain.
This isn’t just about tracking parcels. It’s about connecting supplier timelines, stock levels, shipment status, and delivery performance into a single, navigable flow of information.
Defining the Modern Supply Chain Visibility Model
At its core, supply chain visibility means having continual access to the location, status, and condition of inventory, shipments, and supporting operations—from origin to fulfilment.
However, true visibility goes beyond GPS pings. It means integrating procurement schedules with warehouse readiness, aligning transportation windows with delivery commitments, and managing exceptions before they affect the customer.
Visibility should give you answers to questions like:
- Is the incoming shipment from Jeddah delayed at port?
- Did the inventory update across all sales channels after a bulk return?
- Can we reroute orders from Dubai to a different hub in Abu Dhabi based on weather disruptions?
If you can’t answer these questions instantly, your supply chain is operating in the dark.
The Technology Stack Powering Full-Chain Transparency
Achieving this level of visibility doesn’t happen by chance. It requires a layered approach using dedicated, connected technologies. Let’s explore these systems.
Operations Control Layer: Order Management Systems (OMS)
The OMS is your first touchpoint in creating visibility. It manages orders across channels—retail, B2B, D2C—and ensures each order is properly routed, acknowledged, and prepared for fulfilment.
What a Strong OMS Should Offer:
- Live synchronisation with all digital sales platforms.
- Multi-channel inventory checks before confirming orders.
- Smart routing based on distance, hub capacity, or SLA commitments.
- Status tagging (e.g., awaiting payment, picked, dispatched) visible to customer support and logistics teams.
Platforms like Omniful build OMS systems for multi-region commerce, ensuring order orchestration adapts dynamically to regional constraints and service zones in the MENA region.
Fulfilment Precision: Warehouse Management Systems (WMS)
Once orders are in the system, the WMS oversees all inventory-related operations. It controls receiving, stocking, picking, and packing—each of which affects order accuracy and delivery timelines.
Essential WMS Capabilities:
- Real-time inventory auditing at the bin or shelf level.
- Expiry tracking for perishable categories (e.g., pharma, food).
- Mobile app access for warehouse staff using handheld scanners.
- Zone-specific picking for high-volume or temperature-controlled products.
In MENA, where climate-controlled logistics and dark stores are increasingly common, WMS systems must support multi-location routing and environmental tracking.
Logistics Orchestration: Transportation Management Systems (TMS)
The final mile of visibility happens on the road. A capable TMS ensures your teams (and your customers) know where every parcel is—before the delivery window closes.
Modern TMS Software Should Include:
- Driver and vehicle live location mapping.
- Integration with carrier APIs for automated label generation and tracking.
- Route clustering to reduce travel time and increase fuel efficiency.
- Alerts for delays, failed delivery attempts, or return-to-origin actions.
Platforms adapted for the Gulf’s dense cityscapes and cross-border flows must allow real-time reassignments and capacity balancing between in-house and third-party carriers.
How Real-Time Visibility Changes the Game
Here’s what happens when companies shift from static reporting to live, full-chain transparency.
Better Operational Forecasting
By knowing what’s arriving and leaving in real-time, teams can optimise procurement, avoid overstocks, and reduce write-offs—especially for seasonal or short-shelf-life items.
Smoother Exception Handling
Instead of reacting after a delivery has failed, you can reroute it mid-transit or communicate with customers proactively.
Improved Supplier Accountability
Track which suppliers consistently meet SLAs and which ones frequently miss handover deadlines—then renegotiate or reallocate as needed.
Superior Customer Experience
With parcel tracking updates and short delivery windows now the standard, real-time updates reduce anxiety and create trust.
Region in Focus: Visibility Challenges Unique to the MENA Market
Unlike markets with standardised postal systems and unified road infrastructure, MENA logistics operates with a different playbook:
- Addressing systems vary dramatically between countries.
- COD remains dominant in parts of the GCC and North Africa.
- Urban congestion and rural access both present fulfilment challenges.
- Geopolitical shifts affect border access and customs clearance.
This means generic global platforms often fail to deliver true visibility here. What’s needed are regional solutions with local integrations, flexible routing options, and support for hyperlocal delivery models.
Success Story: Building Visibility from the Ground Up in KSA
Scenario
A fast-growing fragrance group operating across Saudi Arabia struggled with 3PL delays and fragmented warehouse data. Orders frequently missed delivery windows, leading to increased cancellations.
Solution
They implemented an integrated OMS-WMS-TMS platform capable of live synchronisation across hubs and automated order routing based on city clusters.
Results:
- Stock visibility improved to 100% across 8 brands.
- SLA adherence for deliveries improved from 68% to 96% within two months.
- In-house fulfilment reduced logistics outsourcing costs by 40%.
What to Look for When Selecting Visibility Software
Not every platform delivers what it claims. Here’s how to vet a true visibility partner:
Must-Have Feature | Why It Matters |
---|---|
API integration with ERPs and eCommerce | Eliminates siloed data and manual syncing |
Live dashboard access across departments | Empowers ops, customer service, and warehouse teams |
Support for regional routing logic | Adapts to last-mile realities in cities like Amman or Doha |
Auto-alerts for delay triggers | Enables proactive problem-solving |
Data visualisation and export tools | Informs strategic planning and KPI tracking |
What Comes Next: The Future of Transparent Supply Chains
As AI, IoT, and predictive analytics continue to evolve, supply chains are shifting from visibility to intelligent autonomy.
Next-gen trends to watch:
- Smart Contracts using blockchain for supplier accountability.
- Autonomous vehicle routing for warehouse transfers.
- AI bots that recommend alternate fulfilment hubs when stock-outs occur.
- Wearable tech that tracks staff productivity and movement for warehouse optimisation.
Final Takeaway
Visibility is no longer about reducing errors—it’s about unlocking competitive advantage. Businesses that adopt real-time visibility gain the ability to shift resources, reroute shipments, and respond to customer needs with unprecedented agility.
Especially in a region as dynamic as MENA, where consumer behaviour evolves quickly and logistics challenges vary by city, full-chain visibility isn’t just useful—it’s essential.
Frequently Asked Questions
Is supply chain visibility just about tracking deliveries?
Not at all. It includes monitoring inventory levels, supplier performance, warehouse movements, and operational bottlenecks.
How does real-time visibility affect profitability?
It reduces waste, prevents stockouts, improves delivery success rates, and empowers smarter procurement—all of which boost bottom-line results.
Can these tools work with my current ERP?
Most modern platforms are designed with flexible APIs that integrate with legacy ERPs, POS systems, and marketplace platforms.
Are there solutions built specifically for the MENA region?
Yes. Platforms like Omniful are designed with local infrastructure and commerce models in mind, including cash-on-delivery workflows, Arabic interfaces, and dark store support.