Who Gains Most from a WMS? Why 3PLs, Factories & E-Commerce Can't Thrive Without It
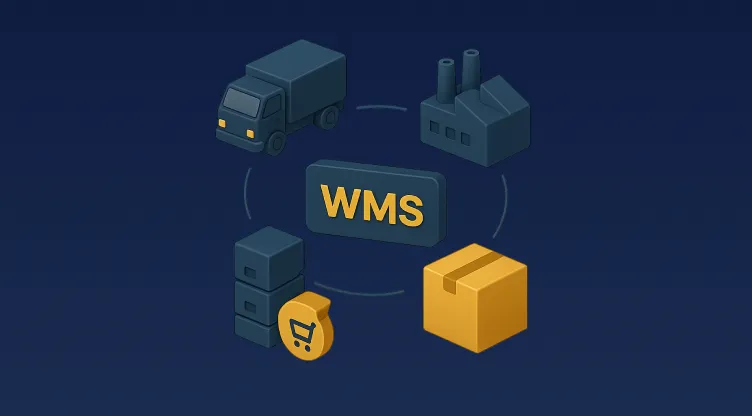
Table of Contents
Fast Track Summary: Who Wins with WMS?
- WMS is a central nervous system for inventory-heavy businesses, helping reduce fulfilment delays and manual errors.
- Logistics providers (3PL) use it to simplify multi-client operations and comply with service guarantees.
- Manufacturers benefit by aligning raw materials, production, and finished goods in a single unified flow.
- Online retailers and e-stores use WMS for real-time inventory visibility, rapid order turnaround, and smoother returns.
- In MENA markets, WMS tools are essential for digitising traditional warehouses and enabling modern retail logistics.
- Platforms like Omniful offer customisable WMS modules tailored to regional operations and regulatory needs.
Introduction: Warehouses Aren’t What They Used to Be
Picture a warehouse a decade ago—static shelves, clipboards, and workers manually counting boxes. Fast forward to today, and that warehouse may be hosting thousands of SKUs, processing same-day deliveries, and feeding data to online platforms in real-time.
This shift didn’t happen on its own. It was powered by smart systems like the Warehouse Management System (WMS)—a backbone technology now critical to logistics success, especially in the competitive and fast-growing markets of Saudi Arabia, the UAE, Egypt, and the wider MENA region.
Whether you're overseeing a factory, an e-store, or a multi-client logistics hub, WMS is the control tower that brings order to chaos. But how does it serve different sectors uniquely? Let’s explore.
Breaking Down the WMS Advantage
Before diving into specific industries, let’s unpack what a WMS really does.
At its core, a Warehouse Management System helps businesses:
- Keep track of every unit of inventory in real time
- Assign storage intelligently to optimise space and reduce retrieval time
- Manage order fulfilment from receiving to packing to dispatch
- Prevent stock discrepancies with automated audits
- Integrate seamlessly with other systems like OMS (Order Management), ERP (Enterprise Resource Planning), and TMS (Transport Management)
Think of it as the digital twin of your warehouse—constantly aware, always alert.
3PL Providers: Making Complexity Look Effortless
Why 3PLs Rely on WMS
Third-party logistics providers face an unusual challenge. They’re responsible not just for their own products, but for the inventories and service levels of dozens—or hundreds—of client businesses. One mistake can hurt multiple brands.
A WMS provides the structure and flexibility needed to juggle multiple sellers, SKUs, and workflows without breaking stride.
How It Helps:
- Isolated environments per client: Ensures each brand’s inventory, pricing, and packing rules are maintained separately.
- Real-time dashboards: Warehouse managers get a live view of pending orders, stock movement, and priority shipments.
- Return handling and billing automation: Automates tedious processes like calculating charges per client, based on space, time, or activity.
Case Insight: Omniful in Saudi 3PL
In the Kingdom of Saudi Arabia, where last-mile expectations are high and logistics costs are under scrutiny, 3PL providers using Omniful have transformed operations. By automating fulfilment for over 100 dark stores, a logistics giant was able to offer next-day delivery promises across Riyadh without bloating their tech stack.
Manufacturers: Building Precision from the Ground Up
Why Production Depends on WMS
In manufacturing, inventory is more than finished products—it’s the lifeblood of the process. A single miscount in raw material stock can halt a production line.
Here, a WMS acts not just as a tracking system, but as a coordinator between procurement, production, and distribution.
Unique Benefits:
- Material traceability: Assigns lot numbers and expiry dates to ensure compliance with quality standards.
- Stock staging: Prepares raw material batches for scheduled production runs.
- Dual unit tracking: Allows tracking in pallets and individual units—useful for conversion-intensive industries like food or pharma.
- Seamless transfer between facilities: Supports internal warehouse transfers for decentralised production flows.
MENA Relevance
As the UAE and Saudi Arabia invest heavily in industrial diversification under their economic visions, many plants are embracing digital systems. A WMS that supports Arabic language, local units of measure, and tax configurations becomes essential in such ecosystems.
E-Commerce: From Click to Doorstep—Fast and Flawless
The Problem Online Stores Face
E-commerce businesses don’t operate in 9-to-5 cycles. Their peak order times might be midnight during Ramadan or during flash sales that last minutes. Delayed orders mean negative reviews, and one stock-out could cost thousands.
A robust WMS levels the playing field between a growing online brand and an enterprise retailer.
Direct Benefits:
- Marketplace sync: Updates inventory across Amazon.sa, Zid, Shopify, and your website in one go.
- AI-picking paths: Uses order clustering and route logic to minimise walking time and speed up order processing.
- Error prevention: Reduces incorrect shipments with barcode validation at packing stations.
- Returns management: Integrates return approvals, inspections, and refunds into one simple workflow.
Saudi Brand Example
One Riyadh-based fragrance brand ditched its fulfilment partner and moved in-house with WMS support. The result? Fulfilment times dropped from 5 days to 3 hours, enabling them to scale their express delivery promise while reducing dependency on external warehouses.
What Makes a WMS a Smart Investment?
Must-Have Capabilities:
Feature | Why It Matters |
---|---|
Mobile Picking | Allows staff to work efficiently using handheld devices |
SLA-driven Workflow | Orders are prioritised based on customer delivery expectations |
Multi-location Support | Helps brands manage dark stores, retail stock, and central hubs |
Plug-and-Play Integration | Avoids lengthy IT projects—connects to your sales and courier platforms quickly |
ZATCA Compliance | Required for invoicing in Saudi Arabia |
AI Optimisation | Saves labour by auto-selecting fastest picking routes |
Whether you're looking to reduce order returns, improve warehouse space usage, or enable multiple shipping providers, a modular WMS helps you plug in just what you need.
What’s Next for WMS in MENA?
The Road Ahead
The next frontier for WMS isn’t just about logistics—it’s about intelligence.
Expect to see:
- Demand-driven restocking: AI forecasts sales spikes and triggers reordering before you run out.
- Visual dashboards: Real-time KPI dashboards showing pick rates, late orders, and workforce productivity.
- Sustainability analytics: Tracking packaging materials, space waste, and energy use for greener operations.
- Integration with robotics: From conveyor belts to autonomous mobile robots (AMRs), WMS will be the brain controlling automation.
In the MENA region, where governments are pushing digitisation in trade, these features will soon shift from optional to expected.
Final Word: Choose Your WMS Like You Choose a Business Partner
You wouldn’t hire a warehouse manager who doesn’t understand your workflow. The same applies to your WMS. Look for a solution built not just for warehouses, but for your specific vertical—be it high-volume fulfilment, precise production, or fast-paced e-commerce.
Platforms like Omniful were designed for the MENA market, offering Arabic support, local tax handling, and integrations with logistics leaders across the region. Whether you’re scaling your operations or just starting to streamline them, now is the time to make WMS your growth catalyst.
FAQs: What People Ask About WMS
Can WMS work with Shopify or Zid?
Yes. Modern WMS systems offer direct integration with platforms like Shopify, Zid, WooCommerce, and others.
Is a WMS useful for small sellers?
Absolutely. Many small sellers grow faster with structured inventory management, reduced errors, and faster fulfilment.
How long does it take to implement a WMS?
With plug-and-play options like Omniful, businesses can go live in days—not months.
Do I need to train my team?
Minimal training is needed. Most WMS platforms offer mobile apps and dashboards with intuitive UX—ideal for warehouse teams.